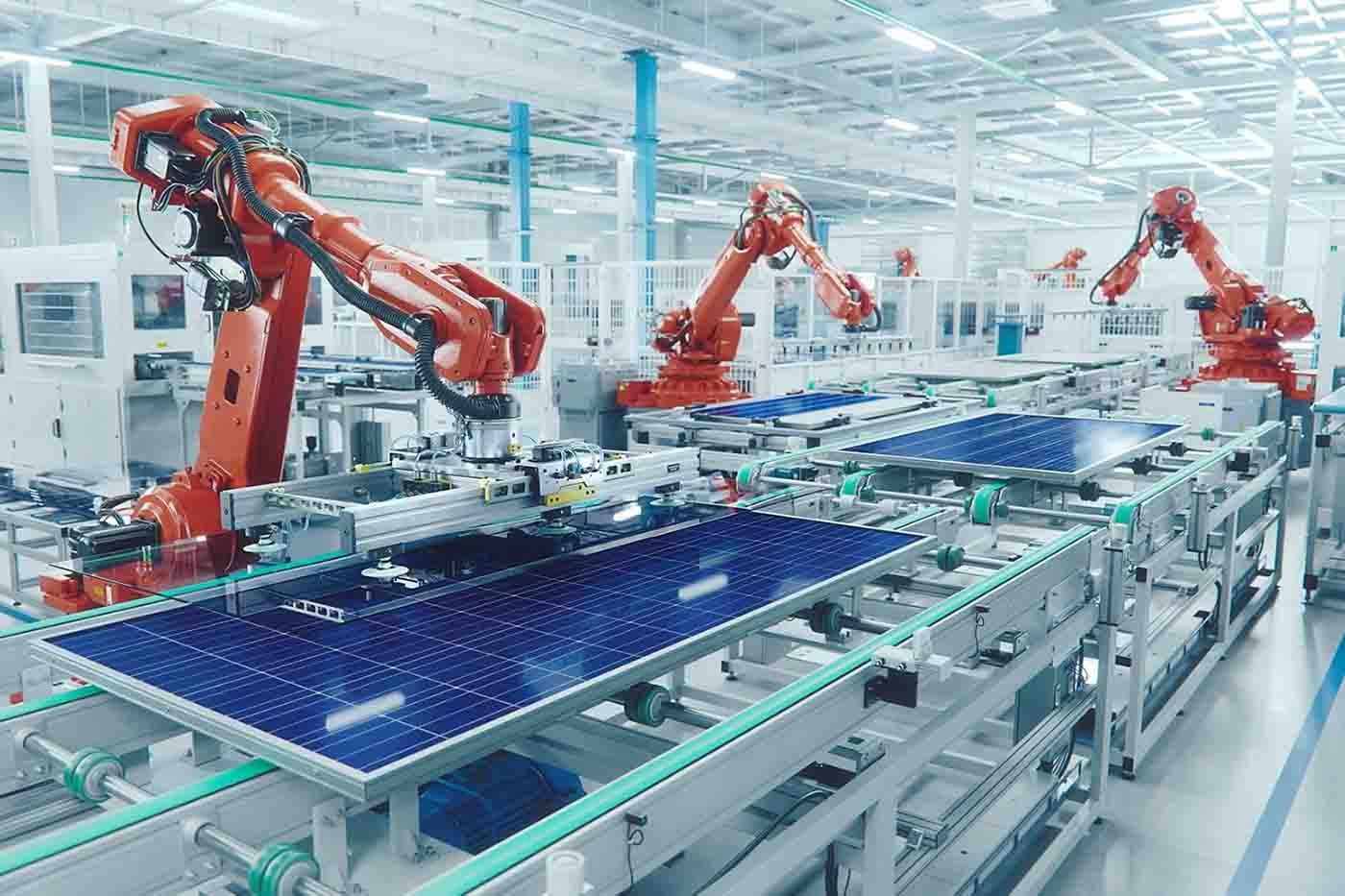
Success in the manufacturing sector is a matter of many factors, but to truly optimize production, efficiency must be a main focus. In the simplest terms, manufacturing efficiency refers to maximizing output relative to the energy input, and there are multiple tricks, methods, and techniques that can be used to do so.
In the following blog post, we’ll discuss what you can do to optimize your business’s production workflow, reduce operational bottlenecks, and improve the overall efficiency of the manufacturing process. We’ll outline simple and straightforward methods you can implement in each step of the process to maximize your output and save on costs along the way.
Take Advantage of New Technology
To truly maximize efficiency in the manufacturing process, it’s critical to take advantage of modern technology, which can help to streamline the production process and reduce or eliminate human error. There are several ways that these advanced technologies are being implemented.
For example, most of the machinery used in modern manufacturing is now equipped with an array of sensors that can track how effectively the machinery is operating. These sensors can detect any maintenance requirements that may arise and alert operators when repairs are required. This can help reduce the downtime that may occur as a result of equipment failure while also avoiding the excessive costs that arise because of improperly maintained machinery.
Automation is also a major element of a modernized production system. By utilizing preprogrammed, automated machinery, manufacturers can ensure consistency and reduce the possibility of defects in the final products.
Make Time for Proper Training
While the importance of technology in the manufacturing process cannot be overstated, even the most advanced production system cannot avoid a human element. Machines used in manufacturing are often assembled, programmed, and controlled by human operators, who must be well-trained to perform their tasks properly. Any individual who utilizes certain equipment should be instructed in its use. Even if it’s not part of their regular roster of duties, supervisors and others who may have to fill in at times should be equipped to operate the machinery.
Ideally, any training for specific equipment should be conducted by the manufacturers to ensure it’s both correct and consistent. For example, at Aberdeen Dynamics, we offer hands-on, industry-tailored training for our machinery. This ensures its correct and effective use, which in turn improves the overall efficiency of related processes.
Identify Weak Points in the Production Process
Any manufacturing is only as strong as its weakest point. That is to say, any flaws in the overall production process will eventually reduce the overall efficiency of the entire operation. Weak points in the production process can lead to operational bottlenecks, which can slow down manufacturing, no matter how streamlined every other element may be.
Poor communication between workers can be a major weak point in any production process. Improving communication should be a major focus of a successful operation, as can occasionally outsourcing tasks to reduce the workload of staff. For example, vendor-managed inventory (VMI) allows the vendor of the machinery to handle tracking and purchasing new inventory with the approval of their clients’ management. This lets your staff focus more on the manufacturing itself.
Inefficiencies in the assembly of the machinery can also lead to operational bottlenecks, particularly if connecting components is confusing or difficult for workers to do. These bottlenecks can be reduced by custom kitting during the manufacturing process. This is the process of pre-assembling and packaging components in a more effective and efficient way to make things easier at the point of assembly.
One simple example of this is the way we package our items at Aberdeen Dynamics: Hoses are packed from top to bottom so that they are removed from the package in the same order they are attached to the machine, saving a great deal of time and preventing any unnecessary guesswork.
Work to Eliminate Waste
A wasteful production process is an inefficient one, and improving manufacturing efficiency is also a matter of eliminating waste. Waste can refer to wasted materials, wasted energy, or wasted time.
This waste can occur on every level of the process. Frequently, defective or damaged parts must be disposed of as a result of inconsistent production techniques, leading to material waste. Wasted energy is the result of inefficient use of electricity or fuel. Time is often wasted as a consequence of the other two problems.
The goal of any effective production process should be to reduce or eliminate waste as much as possible. This begins by pinpointing spots in the process where waste is taking place. For example, if your employees notice that a significant amount of defective output is being discarded, then that is the area to focus on. Similarly, unusually high power costs could signal the need to address and improve overall efficiency.
Once problem areas have been identified, steps can be taken to reduce production waste. Implementing advanced technology, as mentioned above, can help eliminate waste on all levels, as can streamlining communication throughout the manufacturing process.
Invest in Custom Systems
Perhaps the most important step in improving production efficiency is ensuring you are using equipment that is suited to your specific operation. There are no one-size-fits-all machines in manufacturing. Equipment must be custom-made or, at the very least, heavily adapted to the specific industries, companies, and the particular requirements of the individual projects they are being used for. To truly optimize efficiency, manufacturers should invest in innovative, customized systems.
At Aberdeen Dynamics, we integrate custom parts and customize existing parts to ensure they are ideally suited to your operation. We assemble them as much as possible so that they can be attached to your machinery in less time. We add custom fittings as necessary and even paint items to your specifications, allowing your staff to remove items from the packaging and put them straight to use. This reduces the workload of your team, freeing them up to perform more essential tasks. Contact us today to discuss your needs and immediately begin improving your production process’s efficiency.