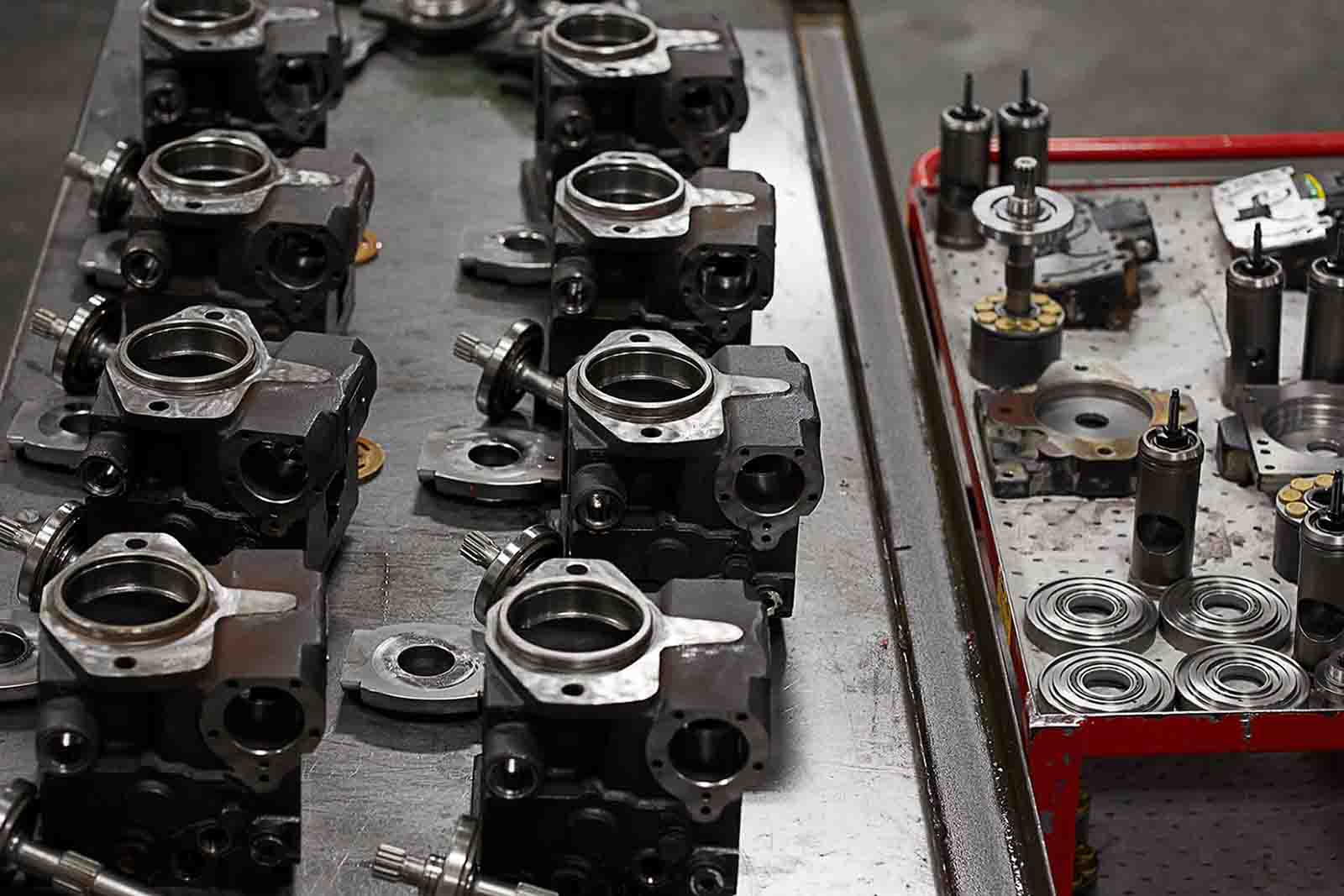
At Aberdeen Dynamics, we offer an extensive list of parts and services, including hydraulic manifold assembly, sectional valve assembly, port adapter installation, electrical connector installation, kitting (combining multiple components under one part number), custom nameplates, and testing and certification to third-party specifications.
Over time and with heavy use, your hydraulic components may require repair or replacement. In addition to the aforementioned parts and services we offer, we also offer complete remanufacturing and repair from our Tulsa, Oklahoma facilities and on-site field services all over.
REMANUFACTURING + REPAIR
Our factory-certified technicians perform hydraulic component repairs to manufacturer specifications. We repair a variety of manufacturer components, including valves, pumps, motors, cylinders, OHLA, and heat exchangers. Each repair includes a one-year warranty on remanufactured components, and we can utilize a three-part epoxy paint on parts if desired.
We also provide repairs for automotive and industrial winches and hoists for top US manufacturers and their specifications, including Braden Winch, Ramsey Winch, Gearmatic Winch, and Lantec Winch. Additionally, we are a Ramsey Winch and Braden Winch authorized service center, where we specialize in total winch service and repair.
FIELD SERVICE
Being customer-minded means we offer ongoing field services, including commissioning, predictive maintenance, field-based training, troubleshooting and repair, and conveyance design.
Commissioning: Our technicians and engineers perform on-site visits to start up your system on-demand or whenever is convenient for you. We can program and tune your electronics to specific applications and provide training for any future adjustments.
Predictive maintenance: We can prevent system downtime by proactively monitoring the fluid cleanliness of your systems, both in real time on-site or in real time remotely. We also perform regular on-site visits to change filters, record performance, monitor cleanliness, and charge accumulators.
Field-based training: We’re proud of the collaborative relationships we have with our customers, including those we work with on-site. Our staff can train your maintenance and operations personnel on various systems to prevent performance recess, allowing issues to be resolved immediately and effectively.
Troubleshooting and repair: We provide an extensive inventory of motion and control components to support systems during malfunction, which gives us the opportunity to quickly correct any issues and minimize interruptions to your business.
Hose and fitting routing design: Our specialists can help optimize hose routing, reduce costs and complexities, expedite installation, and eliminate leak points on mobile and industrial applications, helping your company affordably and conveniently perform better and faster.
Our high-quality parts are made right the first time, but when minimal remanufacturing or repairs are necessary, we offer ongoing maintenance, training, and troubleshooting that can be completed without interrupting the continued success of your business. After all, your success is our business!