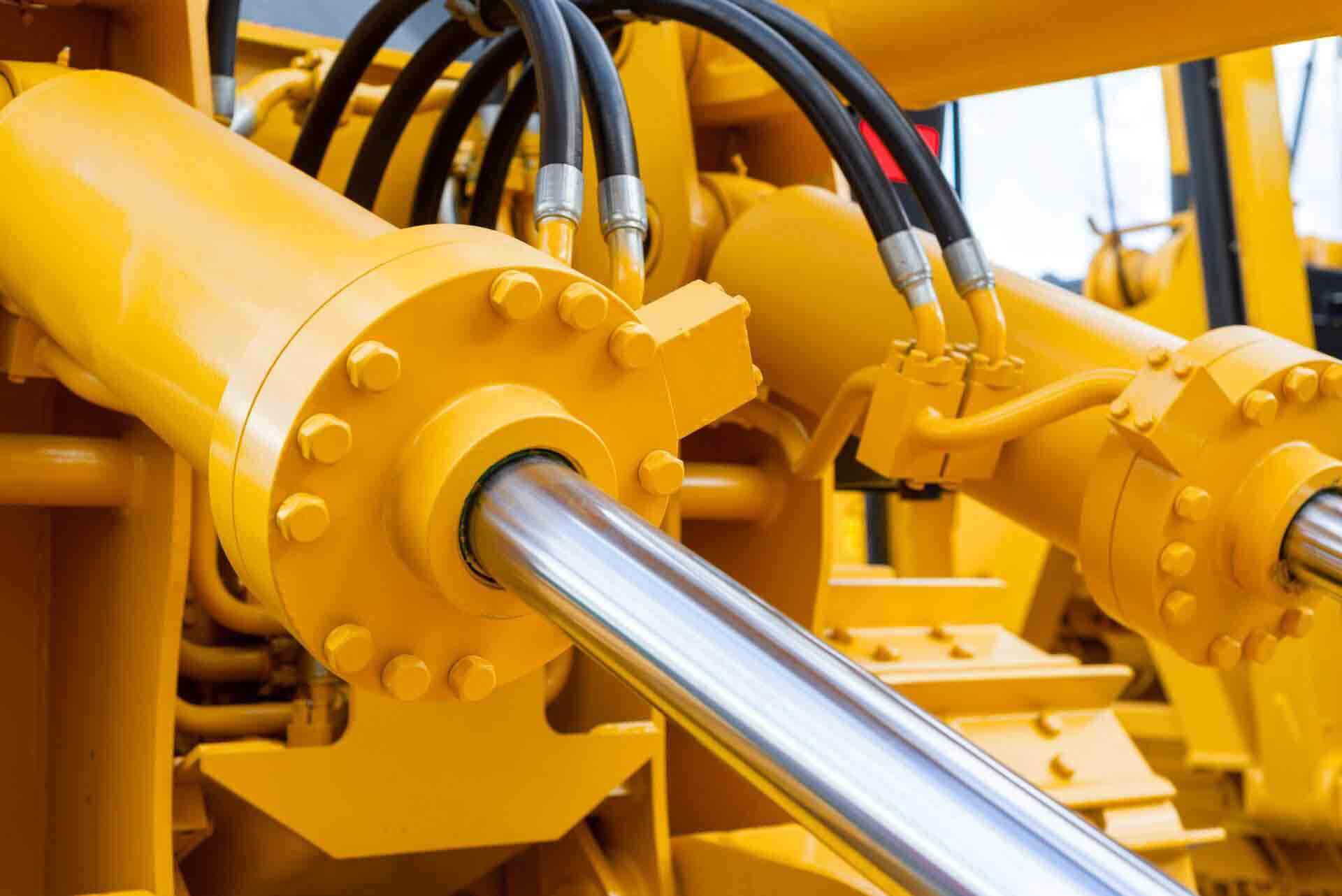
Actuation technology is the basis of many industrial processes, including manufacturing, construction, transportation, and others. It’s this technology that transforms mechanical energy into motion and provides machinery with the power necessary to perform large-scale tasks. Mechanical actuators usually fall within one of two types of cylinders: hydraulic or electric. A hydraulic cylinder is frequently employed for operations that require a high force output, but this style of actuator is not without its drawbacks.
In the following blog post, we’ll outline the strengths of hydraulic cylinders and discuss their advantages over their electric counterparts. We’ll also outline the disadvantages inherent in using hydraulic technology so you can make an informed decision for your specific needs.
What Is the Difference Between an Electric and a Hydraulic Cylinder?
At the most basic level, hydraulic cylinders and electric cylinders are similar types of machinery components. Both are used to generate linear motion for industrial applications, and indeed, the two technologies are sometimes interchangeable, depending on the requirements of the task at hand.
The primary difference between the two types of motion control technologies is in the way motion is produced. A hydraulic cylinder utilizes pressurized fluid to apply force to a mechanical actuator. When a valve is opened by the operator, the pressurized fluid forces a piston to move outward from the cylinder. It can be returned to a neutral position by closing the valve and removing the pressure.
Conversely, an electric cylinder generates linear motion by applying voltage to a rotational motor and then transferring that motion into a ball nut screw that moves a piston back and forth.
Both are effective methods for producing the repetitive linear motion necessary for industrial tasks. However, because of their different methodologies, the applications they are best suited for vary greatly.
Hydraulic Systems Have a Greater Force Output
For tasks that require high levels of force to be output, such as using cranes to lift cargo weighing tons or more, a hydraulic cylinder is almost certainly the best option. That’s because these actuators can take advantage of Pascal’s Principle, which is a physics law that causes all of the pressure applied to a fluid to be applied equally to every point in its enclosed container. This means that incredible amounts of pressure can be generated using a relatively small pump and containment system.
As long as the cylinder is well-constructed and sturdy enough to withstand the vast amounts of pressure produced by pressurizing hydraulic oil, it will be capable of providing the necessary pushing and lifting power for nearly any job. This is a key advantage that this type of setup has over its electric counterpart since an electric cylinder is only as powerful as the torque generated by its motor. Usually, this means that these types of actuators are far more limited in the jobs they can be used for.
They May Be Less Energy Efficient
Energy efficiency is a key consideration for any technology, and this is especially true of the actuator technologies used in manufacturing and other industries. Whenever motion is generated, some energy is inevitably lost due to factors such as friction and redundant movements. When hydraulic systems are used, the pressure must be continuously maintained, even when the system is only idling. This means they are constantly utilizing energy if the system is switched on, which can lead to a great deal of waste. Electric motors are vastly more efficient in this regard, as they only require voltage when the machinery is actively in motion.
While hydraulic cylinders tend to be the least efficient of the two systems, there are steps manufacturers can take to reduce their energy consumption. The first step should be to ensure the correct system is being used for the appointed task. If a hydraulic system is too large or too small for a particular application, then it will use more energy than required. It’s also important that each part of the cylinder is correctly fitted: Poor seals, hoses that are too long, and pumps that regularly fail to generate the appropriate pressure can also limit the overall energy efficiency of the system.
Hydraulic Cylinders Have Improved Durability
In any electric system, there is the possibility of a short circuit or other issues with the voltage. For these reasons, electric cylinders have developed a reputation for being somewhat unreliable. While they are generally fairly simple in their design, there are a few key weak points in an electric cylinder that, if compromised, can cause the system to lose efficiency or even fail entirely. For example, utilizing a motor to provide actuation means that a great deal of strain may be placed on a few elements of that motor; that strain may ultimately cause these parts to become damaged after repetitive use.
One of the main advantages that hydraulic cylinders have over the alternative is their durability. These systems are more powerful, which means each individual element is also more powerful. Hydraulic cylinders tend to be of sturdier construction than other actuation methods due to the fact that they must be built to withstand extreme pressures and rugged conditions. As long as the pump can deliver adequate pressure and the seals and interior workings of the cylinder are in good working order, the system will be able to perform its job continuously and consistently.
Maintenance May Be More Complex
Due to the presence of hydraulic fluid and all the adjunct systems required to contain and pressurize it, hydraulic systems are more complex than other actuation methods. This means they may be more difficult to maintain than other related technologies. Even a slight leak of hydraulic fluid can compromise the effectiveness of the machinery and necessitate a costly repair. The fluid is also at risk of becoming contaminated by air, water, and debris. If this occurs, it may have to be entirely flushed out of the system and replaced before the machinery can be effectively used again.
Many of the problems inherent in maintaining hydraulic systems can be avoided with diligent preventative care. Operators should perform regular inspections of the system so that any potential problems can be addressed before they become more serious problems. If regular attention is paid to the workings of the machinery, then the downtime and costs involved in maintenance will be greatly reduced. If you have further questions about the best actuation technology for your specific needs, or if you wish to have a custom system constructed for your application, contact Aberdeen Dynamics. We specialize in high-end motion control systems, and our team of experts can answer any questions you have on the topic.