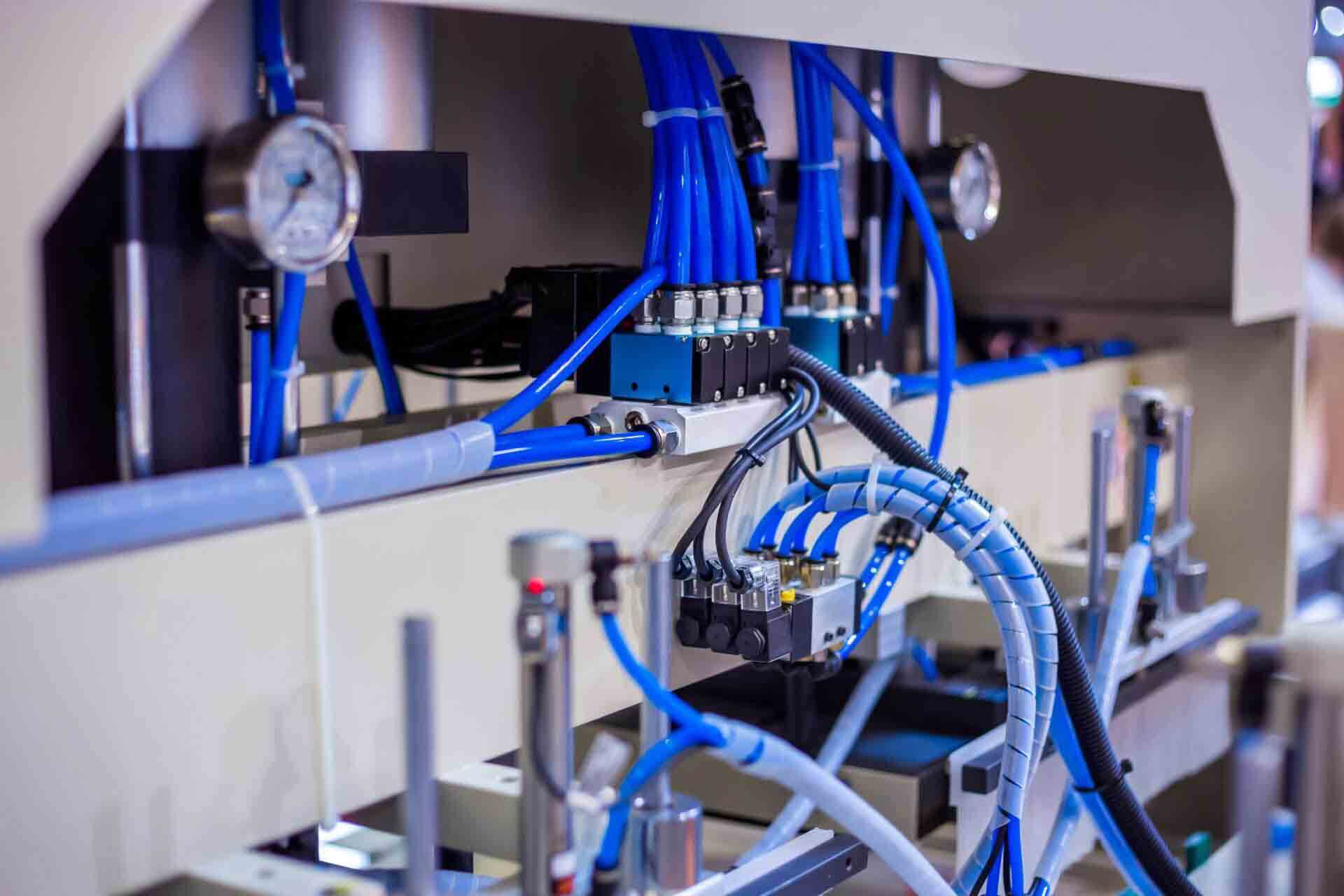
1. Power source
2. Conductors
3. Control valves
4. Actuators
Fluid power systems, which can refer to either hydraulic or pneumatic technologies, are the basis of many different industrial processes. These systems utilize multiple working elements to transfer and control mechanical energy, which allows a wide variety of outcomes to be achieved. Depending on the type of machinery and the purpose for which it has been designed, each system operates differently. However, all of these machinery types have the same four basic mechanisms underpinning their respective functions:
In the following post, we’ll break down each of these core elements and how they enable hydraulic and pneumatic systems to operate efficiently. We’ll discuss the basic function of each, as well as how they work together to allow a fluid power system to achieve the desired results.
1. Power Source
The mechanical energy in a hydraulic or pneumatic system is generated by fluid pressure, which itself is produced by a pump that is built into the system. This pump is controlled by some type of motor that requires a power source. The power source is the first of the basic components we’ll discuss in this article, and there are several possible candidates for providing the required energy for fluid power machinery.
Which power source is best used for a mechanical system largely depends on the size of the machinery. For example, a small pneumatic machine may be able to provide its pump with plenty of power using an electric motor. However, larger systems, such as the hydraulic elements in construction machinery, may require more powerful diesel engines to generate the necessary mechanical force.
Selecting the correct power source for your mechanical system is a matter of weighing that system’s needs: Is raw power key, or is speed more important for your operation? Consider the variables in play, as well as the practicality of the power source you are considering. An electric pump will require a cord and plug, while an internal combustion engine will require a ready source of fuel.
2. Conductors
Once the motor has pressurized the fluid in the power system, the next step is for the machinery to transfer that pressure throughout the equipment, providing it with its mechanical power. The pressurized fluid moves through the system by way of a network of conductors, which include custom-built manifolds and the pipes and tubing through which the fluid travels.
To ensure the correct conductors are used for a particular machine’s specific needs, operators must understand that machine’s specifications and what fluid will be used. Hydraulic oil is often under greater levels of pressure than the compressed air used in pneumatic systems. Therefore, the tubing used to conduct the fluid must be stronger and more rigid. Conversely, pneumatic systems often place an emphasis on speed and dexterity, meaning that flexible hose may be more appropriate for the machines that implement them.
Operators should pay careful attention to the type of material used in the construction of fluid conductors. They must be resistant to the environmental stresses created by the machinery. For example, some materials, such as rubber, may degrade when exposed to hydraulic oil. For that reason, if a flexible conductor is needed, nylon or Kevlar is generally considered to be better suited to a hydraulic power system.
3. Control Valves
Fluid power systems are activated through the use of control valves, which open to allow the pressurized fluid to flow through the conductors in the machinery. As with the other basic components mentioned, there are multiple styles of control valves that differ based on the specific needs of the machinery. Different machines use different methods for opening their control valves, such as utilizing a simple handle versus being controlled electronically by a connected panel.
For systems controlled electronically, solenoid valves are used. These can be opened or closed by applying a current to an electromagnet built into the valve. When the magnet is activated, it causes the valve to open and allows the flow of the hydraulic or pneumatic medium. When the electric current is removed, the valve will close.
For systems that do not utilize electricity as their power source, diaphragm control valves are commonly used. These contain a diaphragm made of a flexible material—usually plastic or rubber of some type—which opens or closes when pressure is applied. They are excellent for both liquid and gas fluid mediums; however, they are rarely rated above 300 psi.
For applications utilizing greater levels of pressure, pinch valves may also be used. These are similar to diaphragm valves, but the flexible internal element is pinched to close the valve. These are better for heavy-duty applications because the flexible material does not contact the fluid medium directly.
4. Actuators
In fluid power systems, the movement of the mechanical parts is created by components called actuators, which transform the energy produced by pressurizing the fluid medium into motion. Actuators may be linear and produce only back-and-forth motion, or they may be rotational and create a turning motion. Actuators are put into motion when the pressure from the system is applied to them, and they can then move other elements of the machinery.
The type of actuator used in a machine depends on that machine’s ultimate purpose, but the vast majority of fluid power systems use single-acting cylinder actuators. These have a simple design that creates a linear motion when the pressure is applied and then automatically returns to a neutral position when that pressure is removed. If rotational motion is necessary, a rack and pinion actuator may be used. This is a similarly simple design that can create torque for turning wheels and other systems where a turning motion is required.To ensure your machinery is operating at peak capacity, you should invest in high-quality materials so each element can work together to generate the movement power necessary for your industrial processes. Contact Industrial Specialties, a certified dealer of Parker Fluid Connectors, to discuss your needs and begin designing the perfect machinery for your needs. You can also visit one of Industrial Specialties’ ParkerStore locations in Oklahoma City or Duncan, OK, for quick access to fluid connectors and more.