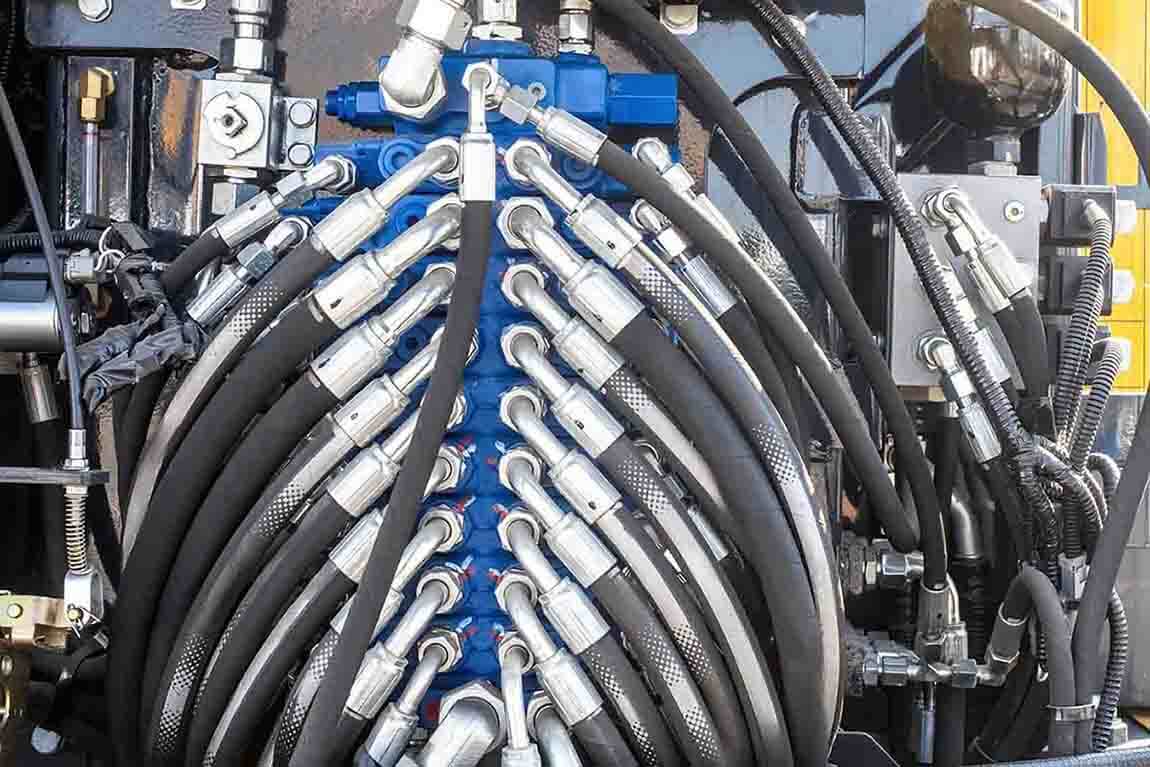
Hydraulic technology is widely used in manufacturing, engineering, construction, and other industries that demand power, precision, and consistency. Indeed, for the largest and most important tasks, this type of machinery is often the only thing powerful enough to do the job. However, even the most advanced hydraulic equipment is only as good as its smallest fitting. Hydraulic fittings create the connections necessary for fluid transfer in industrial machinery, and they are among the most critical elements of functional and effective equipment.
In the following article, we’ll discuss the most common types of hydraulic fittings, as well as their key functions and relative advantages over other types of fluid connectors. We’ll also outline the applications that are best suited to each, helping operators select the correct option for their specific needs.
The Importance of the Correct Fitting
Hydraulic systems generate their power through the use of highly pressurized fluids, which must be able to move unobstructed through the machinery. If any area along the way becomes compromised, whether due to a fluid leak or the introduction of foreign contaminants, then the system will lose a great deal of its efficiency. In turn, this will lead to a vast increase in the energy used by the machinery and reduce the capability of the system to perform its work. Ultimately, it may also cause the technology to fail, preventing critical tasks from being completed until an expensive repair has been performed.
How To Choose the Right Fittings for Your Application
Before making any decisions regarding the type of fitting to be used in your machinery, remember the acronym STAMPED:
- S for size: How large are the hoses the fitting will be attached to? Know the exact diameter before purchasing a fitting to ensure a snug connection.
- T for temperature: Will your fitting be subjected to extreme heat or cold? This is an important consideration when selecting the right material for your connectors.
- A for application: What is the machinery’s specific job? Depending on the application, fittings may need to be permanent or quick-release, among other considerations.
- M for material: Not every material is compatible with every fitting. For example, hydraulic oil may degrade certain rubbers, meaning they won’t make for effective seals. Understand what materials will be in contact with one another before selecting a fitting.
- P for pressure: Different fittings are better suited for different pressure levels. Make sure you select a fitting that is properly rated for the pressures that will be applied to it, including plenty of room for error (that is, do not subject your fitting to the extreme ends of their pressure ratings).
- E for ends: What connection types will be required? There are many common hydraulic fittings, and each has a different method of connecting two hoses together. These will be discussed further below. Ensure you have the proper connection for your specific needs.
- D for delivery: Where will you get your fittings? Are they easy to replace? Anything overly specialized may cause additional downtime as you wait for replacement parts to arrive.
Pipe Fittings
The most basic fitting type used to create connections in hydraulic systems is a pipe fitting. Pipe fittings typically refer to threaded connections, most often NPT (National Pipe Tapered) in North America and BSPT (British Standard Pipe Tapered) in other regions. These tapered threads form a seal by wedging tightly together, often with the help of thread sealant or tape to prevent leakage.
These attachments can be constructed in any number of shapes and sizes and specialized to specific machinery types. They may be large or small, permanent or temporary, and they can be constructed of several different materials, depending on the use.
If cost is a concern, carbon steel is one of the most inexpensive materials a pipe fitting can be constructed from. This material is strong and budget-friendly; however, it is vulnerable to rust, particularly if exposed to moisture or other environmental stresses. Stainless steel is significantly more expensive but also more resistant to corrosion and capable of withstanding vast amounts of pressure. For a fitting that is midrange—both in terms of cost and strength—brass is also sometimes used in the construction of fittings.
Compression Fittings
Besides the material being used, the next consideration users should make is the type of connection that is required. Among the most widely used is the compression fitting. This is one of the most adaptable methods for connecting two parts of a hydraulic system. It is compact and easy to install nearly anywhere while not requiring any tools more specialized than a wrench.
This type of connector creates a seal using a compression ring contained inside the fitting element, which is tightened using a compression nut. This applies enough pressure to the interior element of the fitting to prevent any leakage under most circumstances. Common compression fitting standards include DIN (Deutsches Institut für Normung), SAE compression fittings, and BSPP (British Standard Pipe Parallel) with a compression sleeve. A particular benefit of compression fittings is that they can be used to connect hoses made from different materials, allowing operators more freedom to customize their systems as needed.
Flare Fittings
If your system is expected to be subjected to more extreme pressures, a flare fitting may be the best option for eliminating the risk of leaks. This is a specialized type of compression fitting with a flared end that, when tightened, creates an extremely powerful seal.
The most commonly used flare fitting in hydraulic systems is the JIC (Joint Industry Council) 37° flare, which is widely found in both industrial and mobile hydraulic equipment. For lower-pressure applications, SAE 45° flare fittings are also used.
For connections that aren’t easily accessible, flared fittings are often the best option because they require minimal maintenance. They can also last for years, even when subjected to extreme pressures, vibrations, and environmental stresses.
While the seals they create are unmatched, flare fittings may be more difficult to install than basic compression fittings. They may require specialized tools, such as a flaring kit, to install properly.
O-Ring Fitting
An O-ring fitting, as the name suggests, utilizes a flexible ring made from rubber (or sometimes other materials) to create a seal between the connector and hose elements. Common types include ORFS (O-Ring Face Seal) and ORB (O-Ring Boss) fittings, both of which are widely used in hydraulic systems for their leak-resistant performance under high pressure.
This flexible material has several benefits over alternative options, but it is particularly useful in machinery that will be subjected to a great deal of shock, vibration, and other physical stresses. The rubber material can protect the seal by absorbing the vibrations created by the movement of the hydraulic machinery. This prevents friction caused by metal-on metal-contact, which otherwise would weaken the connection.
O-ring fittings are excellent for the applications mentioned above, but they are not as easy to remove and reconnect as other fittings. The ring itself may become damaged when the connector is removed, necessitating its replacement before reattaching the hoses. To ensure you have the best fittings for your specific needs and to discuss any requirements you have, contact Industrial Specialties, a certified dealer of Parker Fluid Connectors. You can also stop by our fully stocked ParkerStore to get hands-on support and find the right fittings for your application, including JIC, ORFS, NPT, and more. We’ll help to ensure every connection in your hydraulic equipment is operating at peak performance.